sew along

Wrong sides together, pin your seams in place, stitch ¼” in from raw edge.
If you are flat lining your corset, to prevent too much bulk in your seams, trim back the excess, staggering the layers.
Press, and fold right sides together so your first seam is encased. Stitch ⅜” in, and press to one side. Stitching as close to the edge of your seam as you can, top stitch the seam down.
There are lots of layers in there! The boning will get inserted right into these channels. Be precise with your stitching, or it will get tight to put your boning in!
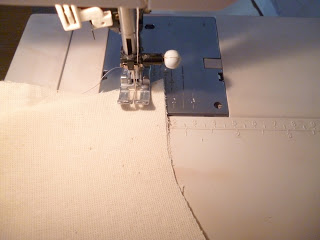
For the laced corset – On the centre back pannel, fold your 2″ extension flap over (towards the inside), press, and stitch 3/8″ in from the centre back edge to form a bone casing, and again 1 1/2″ in from the center back. We will add 2 bones to the mock up corset to test the fit. Insert a bone along the centre back, beside where the corset will lace. Always round off the edges of your boning, to prevent the bone from wearing through your fabric.
For those of you making a hook and eye corset, if you have extra hook and eye tape, you can add some to your muslin to test your fit.
Remember to transfer any changes you made to your muslin, over to your pattern.
Anna wrote an amazing post on grading your corset pattern up or down. You can easily apply her method to any pattern that you are looking to resize.
Head on over to A Few Threads Loose to read Anna’s instructions on Grading your pattern, or read on below…
For those of you that don’t fit into the size range of people I had available to test the corset pattern on, then you’re in luck because I am at your disposal!
First I will show you how to grade to a smaller size, then I’ll show you how to grade to a larger size, though they are very similar.
Keep in mind that you should really make a muslin of this pattern, and you should REALLY make a muslin if you’ve made adjustments like these.
Today we’re going to use reader “E’s” 25″ waist as our starting point.
The smallest size on the pattern is a 29″ waist. (29″-25″=4″).
We’ll need to grade the pattern down 4″ to make it her size.
I like to use centimeters for this (don’t worry, there are centimeters on every ruler and yardstick out there) not because I live in Europe right now, but because it’s just easier than doing a bunch of fractional math all the time.
4″ is 10 cm. (roughly) Now luckily there are only 5 pattern pieces so we know that we need to distribute the 10 cm we’re removing from the pattern at 2 cm per piece.
(4″=10 cm) and (10cm/ 5 pieces = 2 cm per piece)
But wait! These pattern pieces are cut double, 2 of each, so it gets easier! We’re just removing 1 cm from each pattern piece.
Technically there’s just one of the center piece and it’s cut on the fold, but we can still distribute changes the same, as both ends of the piece will reflect the change.
Now we get to the cutting! I’m just going to show you how we’ll do this with pieces 1 and 2 but you’ll do the same with all of them.
Start by cutting the pieces vertically right down the center.
Measure the amount that you want to remove, in this case it’s 1 cm.
Note: if you are removing more than 1 cm form each piece, I know it’s more work but you’ll get better results if you split the pattern pieces into thirds and remove a bit from the inside of each. The same goes for grading the pattern larger than 1 cm per piece.
Next, trim off the amount to be removed from the piece you marked and tape the two pieces back together lining up the top.
At the bottom, you will have a little bit of jagged edge where the pieces don’t quite match up.
This end is a straight line so just line up a ruler between the tip of the pattern piece to the inside where it should match, mark, and then trim.
Do the same with each pattern piece.
To grade the pattern piece larger is a really similar process.
Reader “A” has a 37″ waist and also asked this question. That’s lucky because it’s another 4″ difference between the size she needs and the largest size on the pattern.
Using the same math from above, we know that we need to add 1 cm to each pattern piece.
(4″=10 cm) and (10 cm/ 5 pattern pieces = 2 cm per pattern piece, cut double, = a 1 cm adjustment)
I’m going to use piece # 5 to illustrate.
As with grading down, to grade up we split the pattern piece vertically down the center.
When I cut out a digital pattern, I always keep a handful of my paper trimmings from taping them together on hand for alterations like this.
I have measured and cut a strip 1 cm wide.
Place the piece in between your split pattern pieces and tape it back together.
Trim smooth the jagged edges and you’re ready to do it to the other 4 pieces.
Voila! Any questions?
The question is, are you wearing it to the bedroom or the boardroom?
Boning your corset is always best, to be honest. In my experience, unless it’s hiding under a dress, bedroom lingerie has a shelf life of about 2.5 minutes before it lands on the floor. That 2.5 minutes doesn’t require too much support. The main point of the side boning in this corset is to keep it from folding and bunching up on you when you bend over.
(I’m sorry, I’m immature, and I’m giggling at all the double entendres as I write this.)
There are several kinds of boning that you can use both new and vintage.
Vintage Notions:My mother, the fantastic vintage dealer and former custom corset-maker literally has buildings full of vintage clothing, patterns, ribbon, fabric, notions and a million other things. Last summer on a visit home she and I dug through boxes and boxes and I stumbled across more than one large box that was overflowing with old bias tape, rick rack, needles, ribbons, spools of thread, and to my delight, a box of Warren’s Featherbone.
Needless to say, I bought an extra suitcase to drag the contents of the box home with me.
Since I’m using vintage satin and lace, it’s obvious I need to throw some vintage boning in the mix.
The Featherbone seams to be a somewhat flexible fiber and plastic composite material already covered in a neatly stitched casing.
It’s not too easy to find but so far I love working with it. There’s a box of it for sale here.
Spiral steel boning is made of a flattened, coiled metal. It is very flexible, and can be purchased by the yard or in pre-cut lengths. Spiral boning comes in different widths – the wider the bone, the more supportive. Spiral boning works nicely to shape the sides of corsets. When buying yardage of this type of boning, you will need to purchase bone tips to cover the raw ends of the bones.
Spring steel bones are very rigid, plastic coated metal bones. These are are very strong bones that are somewhat flexible, but do not easily bend. Spring steel bones come in differing widths and thickness. The thicker the bone, the less flexible it will be. Spring steel bones are great for putting on either side of your lacing, to help reinforce your eyelets, or down a flat front corset.
Plastic boning is the most common type of boning. It comes in different densities and thicknesses. Regular Plastic boning (sometimes called featherweight) is a thicker boning, that generally comes in ¼” widths. Rigilene boning is a lighter weight boning that can be easily sewn through, and tacked into place. Either type of boning is suitable for the corset girdle. Plastic boning is quite flexible, but can retain bends, unlike spiral steel boning. Most plastic boning is sold in a casing.
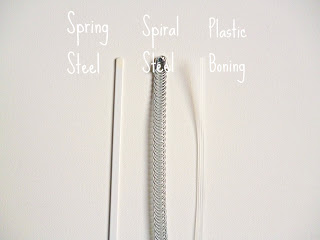
http://www.farthingales.on.ca/ Canadia corsetry and costuming supplies.
http://www.corsetmaking.com/ a US Based corset supply retailer.
http://www.venacavadesign.co.uk/ a UK Based corset supply retailer.
More on your muslin next.
Ooh La La Pin Up Sew Along: Printing Your Pattern & Adding Seam Allowances
Uncategorized February 21, 2012Print out your corset garter belt pattern on regular, letter size paper, making sure the printer scaling is at 100%. Arrange each piece on a large work space. Cut and tape each corresponding piece together, like so:
For corsets that will lace – add 2″ to the centre back seam. This will form a facing. We will also need to draft an interfacing piece to reinforce this section.
Why do you need to face and interface this section? There will be a lot of pull on the grommets – if they are set through 1 layer of fabric they are going to work their way through in no time. You will also want to add boning along either side of the eyelets to prevent “scrunching” (ick!), and the facing will form your bone casing.
Measuring in 2″ from the centre back line, draw a line straight up (parallel to the centre back line).
Anna wrote a great post on what you will need to prepare for the Corset Garter Belt Sew Along.
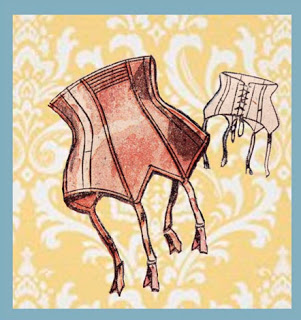
I am so so so excited! Anna, from A Few Threads Loose, came to me with a great idea – a co-sew along! If you haven’t seen Anna’s Etsy shop yet, she sells the best selection of vintage patterns and pdfs.